
Solution for more sustainable plastics: Neste RE™
Our approach to enabling the plastics industry’s transition away from fossil is simple: change the source of the carbon, not the product or its characteristics. Our feedstock for plastics, Neste RE™, does exactly that.

Benefits of Neste RE
Helps reduce fossil resource dependency
Helps reduce carbon footprint of plastics and chemicals
Helps reduce scope 3 emissions
Doesn’t change product properties
Doesn’t require changes to production infrastructure
Fossil resources leave a significant carbon footprint for plastic products. By 2050, plastics could make up 20 % of global oil and gas consumption and account for 2.8 gigatons of GHG emissions per year*. It is clear that in striving for net-zero emissions, the use of fossil resources in plastics must be reduced significantly.
*CIEL: Plastic & Climate: The Hidden Costs of a Plastic Planet, 2019
Petrochemicals have alternative solutions available
Renewable raw materials
Biomass can be turned into high-quality plastics feedstock due to its high carbon content. This renewable (or “biogenic”, “bio-based”) carbon can be used in plastics value chains, replacing fossil carbon and improving the carbon footprint of plastics. It can help companies in the plastics value chain to reduce their scope 3 emissions.
Recycled raw materials
Plastic waste can be a valuable source for carbon, as well. In principle, plastics can be recycled to create new plastic products. As recycled carbon derived from plastic waste can replace virgin fossil carbon in plastics production, this allows us to keep the carbon circulating, reducing the need for virgin raw materials.
The difference is in the source of the carbon: Our product Neste RE is made with renewable and recycled raw materials. Instead of fossil resources, we use sustainability certified bio-based materials, e.g. waste and residues such as used cooking oil, and recycled raw materials such as plastic waste, to produce Neste RE.
Neste RE not only reduces the need for fossil resources with their heavy carbon footprint, but also adds value to plastic waste, contributing to keeping materials circulating and combating plastic waste pollution.
Change the raw materials, not the product
Fossil feedstock can be replaced with Neste RE without changes in the polymers and chemicals manufacturing infrastructure. Plastics based on Neste RE are of identical quality to those made from conventional feedstock. They can be turned into exactly the same products and used for the same applications – and recyclability of plastics made with Neste RE remains the same, as well.
What changes is the carbon footprint of the products. Independently reviewed life cycle assessments (LCA) for Neste RE capture the benefits in numbers:
Neste RE based on renewable raw materials can reduce greenhouse gas (GHG) emissions by more than 85% when replacing fossil feedstock*.
The use of Neste RE produced from plastic waste reduces GHG emissions by more than 35% when compared to a conventional scenario in which feedstock for plastic is produced from fossil materials and plastic waste is incinerated instead of chemically recycled**.
*Life Cycle Assessment on Environmental Impacts of Neste Renewable Polymers and Chemicals (30 June 2021) **Life Cycle Assessment on Environmental Impacts of Chemical recycling of waste plastic - Case Neste (October 2022).

Renewable raw materials
Neste RE utilizing bio-based carbon is a solution for plastics producers wishing to reduce their products’ carbon footprint and their reliance on fossil resources.
We can offer two ways to produce Neste RE using bio-based raw materials:
Route I: A segregated process via our renewable products refineries utilizing our proprietary NEXBTL technology.
Route II: Co-processing of bio-based materials in our oil refinery and applying mass balancing.
Route I: The NEXBTL process
Transforming renewable raw materials such as waste and residues into Neste RE: a premium-quality, renewable feedstock for polymers and chemicals.
For the production of renewable Neste RE, we are leveraging Neste’s proprietary NEXBTL (“Next generation biomass to liquid”) technology. NEXBTL enables us to turn bio-based oils and fats into pure hydrocarbons: fuels or feedstock for plastics and chemicals production. Waste and residue oils and fats, such as used cooking oil or waste and residues from vegetable oil processing, account for more than 90% of our annual renewable raw material inputs globally.
Production of Neste’s renewable products has three steps: pretreatment, hydrotreatment and isomerisation. The output is a variety of renewable products from 100% renewable raw materials.
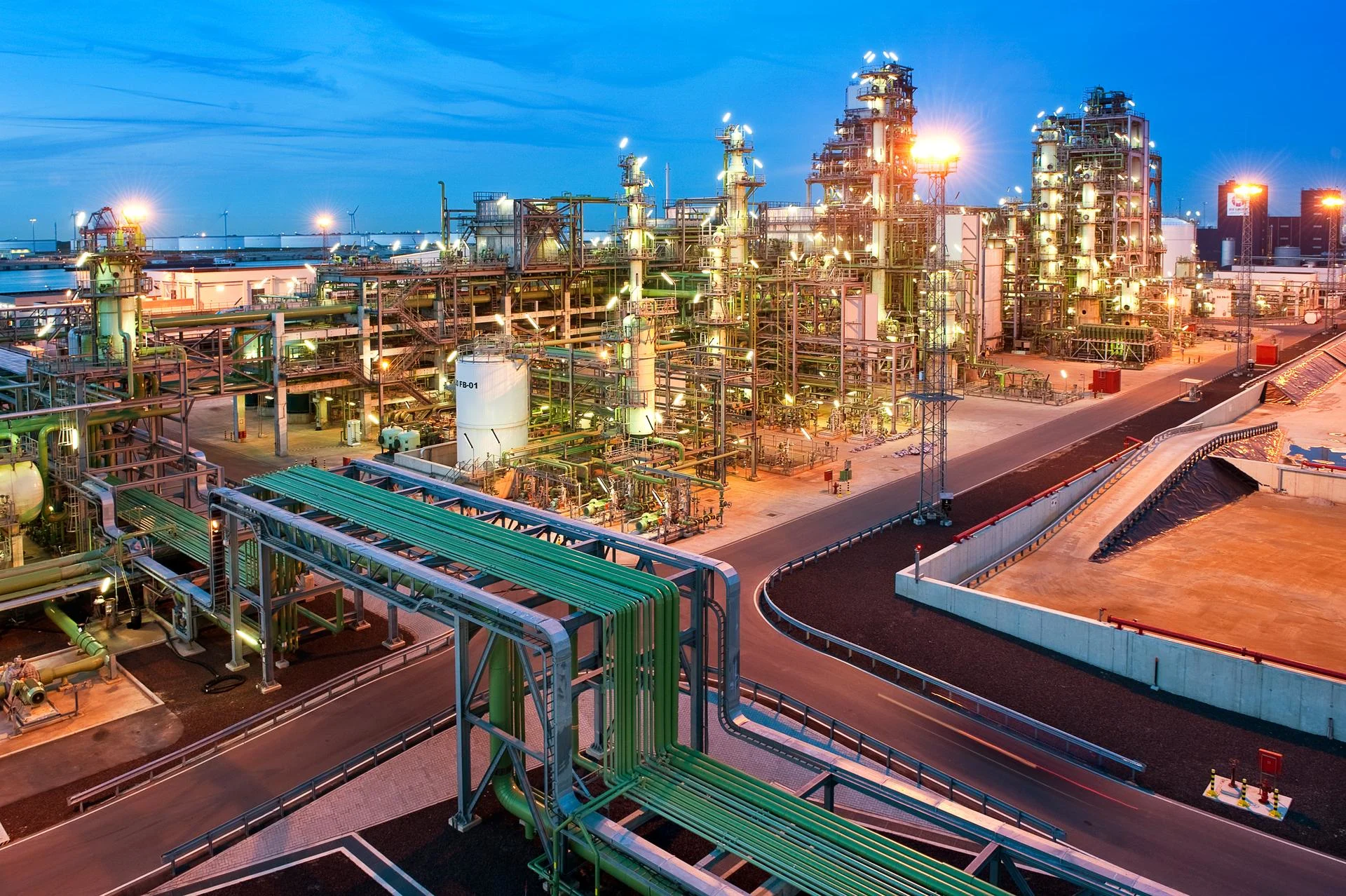
Route II: The co-processing approach and mass balancing
Renewable raw materials can also be processed together with fossil crude oil.
Our oil refinery in Porvoo, Finland, is capable of co-processing renewable raw materials together with fossil crude oil. The output can replace conventional fossil raw materials for plastics such as fossil naphtha or propane without any concessions to quality.
For co-processing, we are applying the mass balancing method: In the refinery, renewable raw materials – such as waste and residue oils like used cooking oil – are mixed with fossil crude oil. The output is a product consisting of both bio-based and fossil molecules. The exact composition of a specific batch may vary: It depends on the input ratio.
Mass balancing concept is based on tracking the share of bio-based and fossil material inputs and allocating the respective bio-based content to the volumes of the manufactured products.
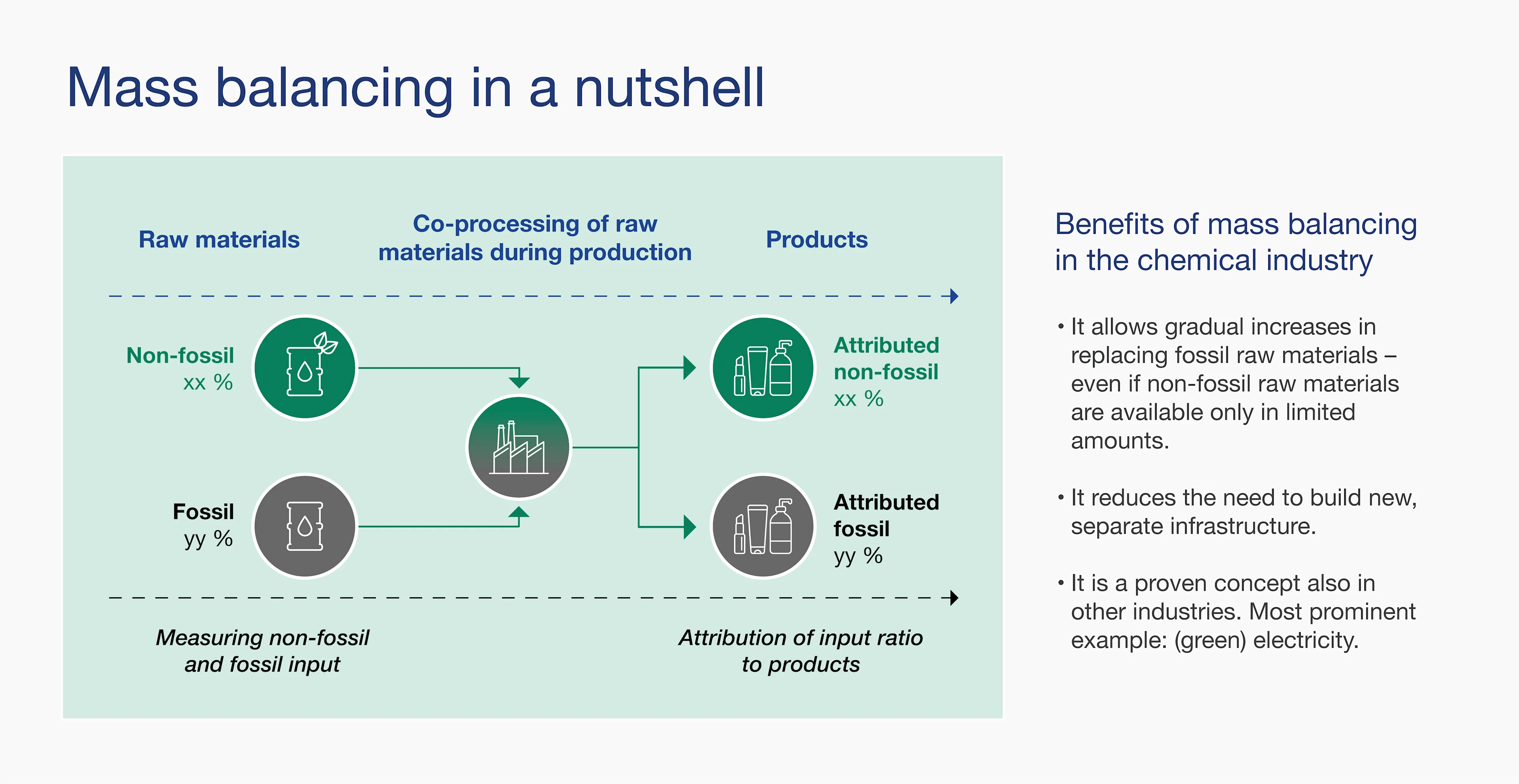
Mass balancing is a useful concept when there is no difference in quality or performance of different materials used, as is the case with Neste RE. It allows for a gradual transition from fossil to non-fossil materials in the value chain. Once there is sufficient supply of non-fossil materials to run entire value chains just on non-fossil materials, mass balancing is expected to become less relevant.

The impact: significant reduction in GHG emissions
Using renewable raw materials to replace fossil raw materials in the polymers and chemicals industry can significantly reduce GHG emissions over the lifecycle.
The benefit of replacing fossil feedstock for plastics with renewable feedstock lies with the carbon footprint. Renewable feedstock consists of renewable carbon from the atmosphere that has been absorbed during biomass growth. When this carbon is later released back into the atmosphere, e.g. when plastic produced from renewable feedstock is being incinerated, it does not add additional carbon to the atmosphere. Instead, the carbon is part of the natural carbon cycle where carbon is continuously exchanged between biosphere and atmosphere.
Using Neste RE produced with renewable raw materials therefore comes with a significantly reduced carbon footprint over the use of fossil resources.
For example, our life cycle assessment (LCA) shows a greenhouse gas emissions (GHG) reduction of more than 85% when renewable Neste RE feedstock from NEXBTL replaces fossil feedstock*.
*Life Cycle Assessment on Environmental Impacts of Neste Renewable Polymers and Chemicals (30 June 2021)

Recycled raw materials
Plastic waste can be a valuable resource. In principle, plastics can be recycled to create new plastic products. This allows us to keep the materials circulating, reducing the need for virgin raw materials.
However, only less than 10% of global plastic waste gets recycled*. Our goal is to change that and make sure that more materials are kept in the loop. Our solution to do so is recycled Neste RE: pure hydrocarbons made from waste plastic, which can be used to produce virgin-quality plastics again.
There are multiple reasons for the dismal recycling rate of less than 10%. One is a lack in collection and sorting of plastic waste. There are huge differences between regions and countries when it comes to the infrastructure to collect and sort waste. Another reason is that some types of plastic waste are easier recycled than others.
*Global Plastics Outlook World, OECD, 2022
The approach: chemical recycling
To produce recycled Neste RE, we are using a new technology: chemical recycling.
Today’s predominant plastic recycling technology is mechanical recycling. While it is a very efficient process, it relies on rather clean plastic wastes. Further, it also slightly diminishes the quality of the recycled material, leading to a finite amount of possible recycling cycles. Finally, there are also limitations in the applications that can be made from mechanically recycled waste plastic: The more sensitive the application (e.g. medical or food contact), the more difficult it becomes. For certain waste streams though, e.g. PET bottles, mechanical recycling is a very valuable and important approach to circular plastics.
To produce recycled Neste RE, we are using a new technology: chemical recycling. While mechanical recycling maintains the polymeric structure of the plastics, chemical recycling works similar to a reset button. It turns the wheel back a little further by breaking up this structure and thus turns the plastic back into the raw material (hydrocarbons) it was made of.
The plastic waste we use as a raw material is liquefied by our suppliers, creating a liquid that to some degree resembles crude oil. Dedicated processes in our conventional oil refinery then remove various impurities and turn the liquefied waste plastic into high-quality feedstock for new plastics again. This feedstock, Neste RE consisting of pure hydrocarbons, is of virgin quality and can be turned into all kinds of plastics for varying applications. As of today, the liquefied waste plastic is co-processed in our refinery together with fossil crude oil, applying a mass balancing method.

The advantages: with chemical recycling, we can recycle plastic waste that currently has no real use as it is considered hard to recycle with conventional means. At the same time, chemical recycling also leads to virgin-quality raw materials for new plastics, so there are no concessions to quality, purity or sensitivity versus plastics made from virgin raw materials: Chemically recycled feedstock can be used for all kinds of plastic applications, including sensitive ones like food-contact packaging or medical products.
While chemical recycling requires more effort and more energy than conventional recycling, it tackles different waste streams and turns them into a different output. That is why we consider mechanical and chemical recycling complementary technologies – and we will require both to tackle the plastic waste challenge.
The impact: more than 35% reduction in GHG emissions
More than 35% reduction in GHG emissions over the life cycle compared with when plastics are made from fossil resources and plastic waste ends in incineration.
Our independently verified life cycle assessment (LCA) shows that despite the efforts required, chemical recycling can contribute to improving the carbon footprint of plastics when it replaces the use of fossil resources and the incineration of plastic waste. In fact, GHG emissions can be reduced by more than 35% if recycled Neste RE replaces fossil feedstock and prevents plastic waste from being incinerated*.
* Life Cycle Assessment on Environmental Impacts of Chemical recycling of waste plastic - Case Neste (October 2022).
Replacing fossil feedstock with Neste RE can be done without changing the infrastructure. Plastics based on Neste RE are of identical quality as those made from conventional feedstock. They can be turned into just the same products and used for the same applications - and the recyclability of plastics made with Neste RE remains the same as well.
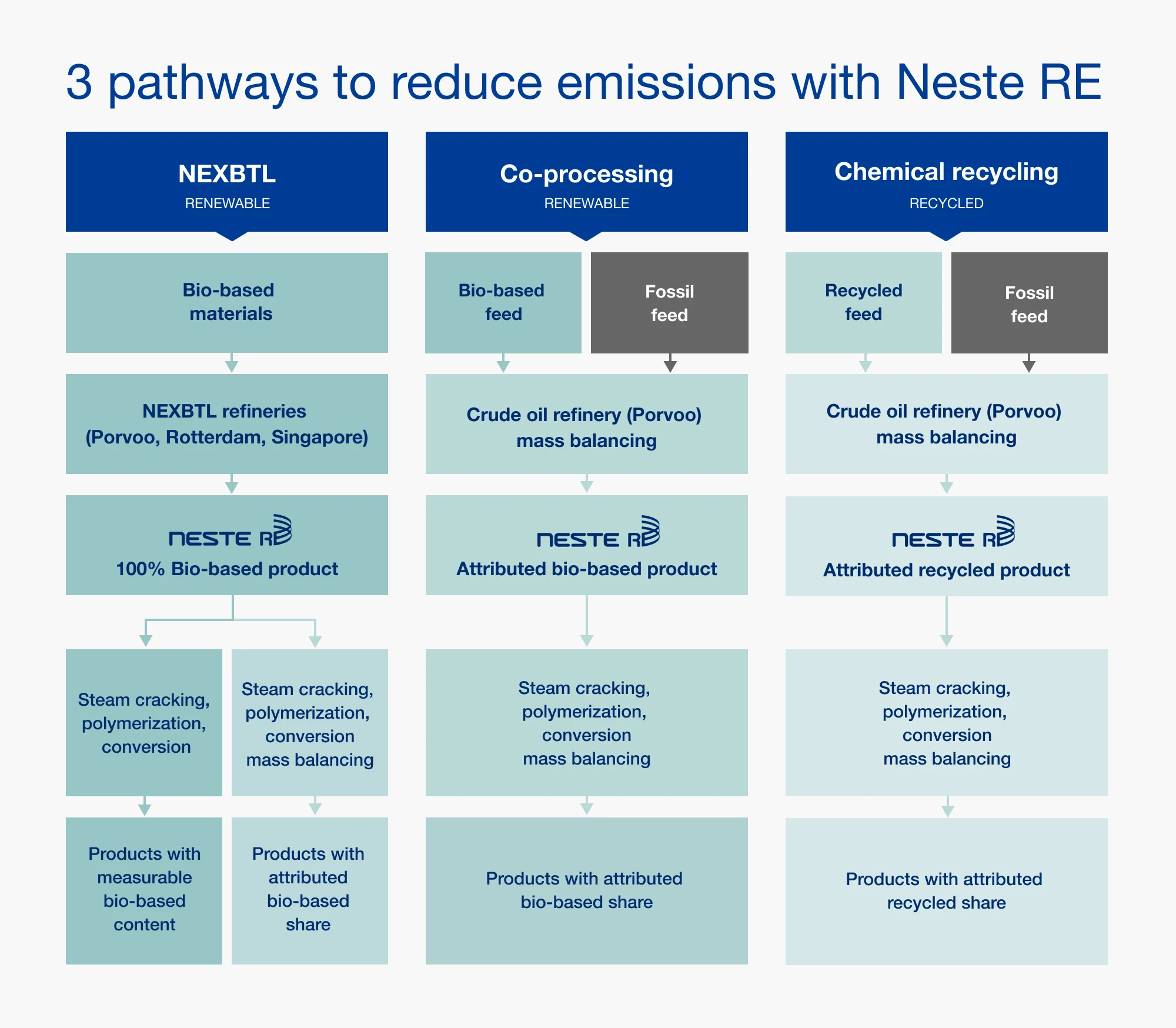